Wearing screeds, widely known by the former name of granolithic screeds, are high-density toppings suitable for application to green or hard concrete slabs. Offering characteristics desirable for areas likely to be subjected to severe wear and heavy traffic, these toppings are the preferred choice for industrial flooring projects.
Granolithic screeds consist of cement, sand and crushed rock aggregate, such as granite, limestone and quartzite, in a 1:1:2 ratio. Since granolithic toppings have a higher resistance to abrasion and impact than traditional cement-sand screeds, they can be used in a variety of industrial applications as wearing surfaces without final floor coverings.
Traditionally, granolithic finishes are used in applications where a sound, consistent, hard-wearing yet inexpensive surface is required (e.g. service corridors, warehouses, plant rooms, power stations, weight-lifting areas, etc.). Granolithic toppings should be laid at 15 mm to 20 mm depth, directly on to fresh concrete before setting has commenced (monolithic construction), or to a thickness of 25 mm to 40 mm, bonded to hardened concrete slabs.
Granolithic screeds are not suitable for unbonded constructions. In applications where bonding is not possible, a new concrete slab typically 100 mm thick should be installed and the screed laid monolithically on top.
Though granolithic toppings can be used in conjunction with underfloor heating, extra caution is required as excessive drying, cracking and curling can occur, especially when the commissioning cycle of the underfloor heating system has not been performed correctly.
Since these screeds are typically mixed on site, specific issues such as incorrect mix proportions, batch-to-batch variations and inadequate mixing can lead to adhesion and compaction problems, making the screed more prone to cracking, curling and debonding from the base. To prevent screed failure, the screeder must comply with the recommended cement-aggregate-water proportions and use the right mixing techniques (e.g. forced-action mixing instead of hand mixing).
Additionally, the builder must ensure that the right mix proportions are provided for the concrete slab to develop the strength required (minimum 35N/mm2, as per BS 8204-1). In bonded constructions, proper preparation of the substrate is critical to guarantee optimal bonding and long-lasting performance.
Though the performance and lifespan of granolithic screeds depend on the type of aggregate used, screed thickness, quality of finishing, curing and drying, screeders can enhance resistance to cracking, abrasion and wear by adding polymers and PP fibres to the screed mix.
Another point worth mentioning is that granolithic toppings provide a rougher surface than other types of screeds. However, they tend to wear smooth and lose slip resistance over time. To improve the level of slip resistance, an abrasive grit can be incorporated into the screed. The screeds that have become slippery can be treated mechanically or chemically to provide a rougher surface.
Two major advantages of using these toppings are that they are unaffected by dampness and require minimum maintenance, which usually implies the removal of dirt with hot water and detergent, and repairs or replacements of damaged areas with epoxy resins or granolithic finishes.
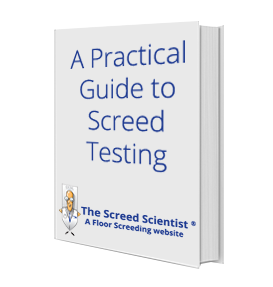
WHY SCREED TESTING CAN SAVE YOUR PROJECT TIME AND MONEY?
Download your free Practical Guide to Screed Testing here.